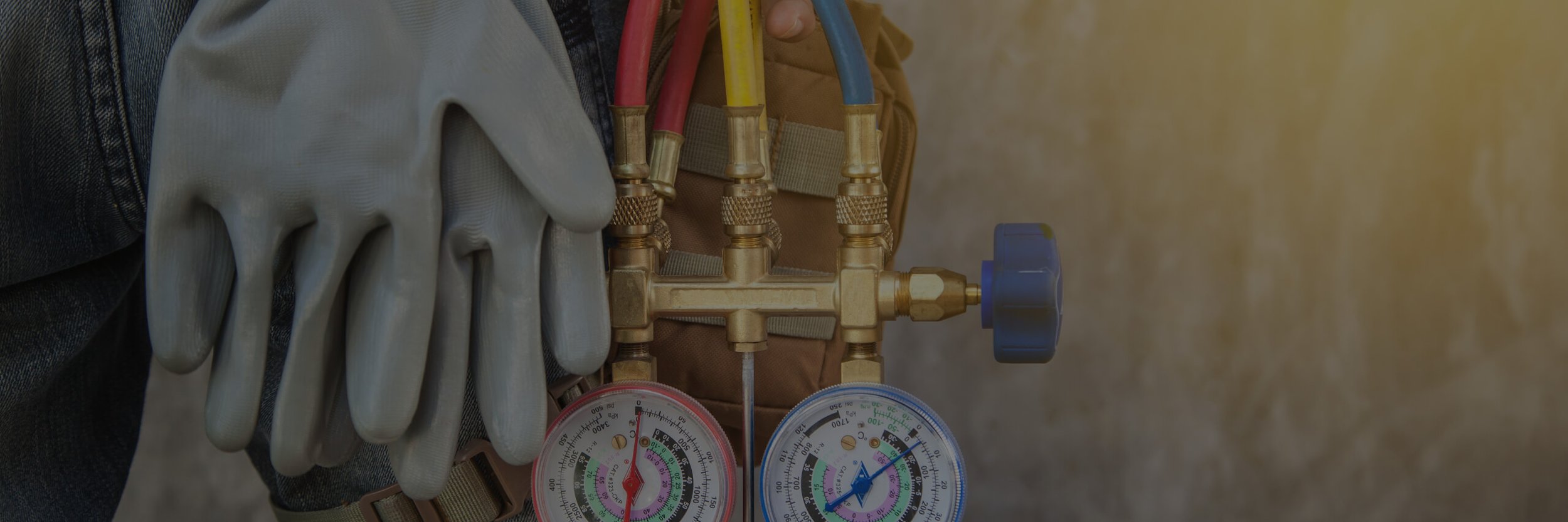
How To Use Gauges Properly
EPA 608
EPA 608: How to use Gauges Properly
The use of gauges is essential for effective and precise calibration, removal, and charging of systems containing refrigerant. The most common machinery requiring gauges are usually air conditioning systems, heat pumps, and automobiles. While automotive will be covered later, heat pumps and AC units require precise gauges and measurements to ensure proper and efficient function. You will never see an HVAC technician without a set of gauges working on an HVAC ac system.
No matter what gauges you have, digital gauges or analog, make sure the gauges are calibrated and in good working condition. Gaskets often fail and can leak refrigerant while the system is operating. As a precaution, changing them every few times you hook and unhook from a system can lead to much better results.
Every gauge system consists of hoses, valves, gauges, and a manifold. A manifold is where everything is connected simultaneously. It’s this area where a user can attach additional equipment, connect hoses, and add or remove refrigerants. Before even attempting to use your manifold gauge, ensure all the valves and knobs are closed. It’s also a good idea to add a check valve at the end of each hole, so you can isolate the gauges from the operational unit itself.
The next step is to attach the manifold gauge to the refrigerant system through the pressure hoses according to the manufacturer's instructions. The low-pressure side, or suction side, is typically indicated by a blue hose, and the high-pressure side, or high side is indicated by a red hose. Refrigerant charge is usually added via the yellow hose. Sometimes there will be an additional black hose that many use to vacuum pump down a system to a specific micron or reclaim refrigerant.
Turn off the power to the system and open the access valves on the manifold gauge set. Now is the time to connect the hoses to the service ports. It’s typically straightforward to attach the hoses and does cause a little refrigerant to leak out when connecting to the system piping. Having a check valve between the system piping and the hoses reduces the possibility of a hose or manifold failures leaking excessive refrigerant out of the system. A release of too much refrigerant can lead to the compressor and reversing valve becoming damaged as the system works harder to compensate for the loss.
Start the refrigeration system and allow it to run for a few minutes to let the refrigerant pressure stabilize. Every refrigerant will have associated measurements corresponding with the mix. While most will require PSI, it’s not uncommon to see megapascals or MPa. Make sure you have the proper readout for your gauges as ‘on the fly’ conversions are not possible since the measurements are constantly changing.
Check the pressure on the gauges. The low-pressure gauge should read the pressure on the suction side of the refrigeration system, and the high pressure gauge should read the pressure on the discharge side. Again, blue is typically associated with low pressure while red is associated with high pressure. When working on a heat pump with a reversing valve these measurements can flip back and forth, depending on the valve placement inside the compressor.
Compare the pressure readings to the manufacturer's specifications to determine if the system is operating within the recommended range. As an example, R-410a has a minimum required PSI of 370 PSI read on the gauge set to generate heat for a heat pump. Different refrigerants have different measurements, and various HVAC systems will also have specific recommendations. If the pressure readings are not within the recommended range, adjust the system accordingly. For example, if the low-pressure is too high, you may need to add refrigerant to the system. If the high-pressure side is too low, cleaning the condenser coils or check for other problems become essential. Gauges are employed for diagnosing, troubleshooting, and charging purposes. Any other work on a unit will require systems not associated with the gauges.
When you are finished using the manifold gauges, turn off the power to the refrigeration system and close the access valves on the gauges. Remove the gauges from the system and store them in a safe place. Keep in mind; there may still be refrigeration left in the hoses after disconnecting, especially if using check valves. There are also low loss fittings which help reduce the amount of refrigerant being removed from the system via the hoses. This type of refrigerant loss is called Loss De Minimum by the EPA. As they state: “‘De minimis’ quantities of refrigerant released while making good faith attempts to recapture and recycle or safely dispose of refrigerant including releases that occur when connecting or disconnecting hoses to charge or service appliances.”
If you would like to be able to safely and effectively work on refrigerated systems and put these skills to the test, we provide EPA 608 certification. This certification will teach you all about various types of refrigerants, the refrigeration cycle, and the EPA standards surrounding refrigeration materials. It puts you in a position to be more valuable and skilled. It’s an essential license for HVAC which allows any license holder legal and safe handling instruction of refrigerants.
Learn more about our A2L Refrigerant Certification, as well as our EPA 608 Certification and EPA 609 Certification programs.